Soil Stabilization Methods and Materials
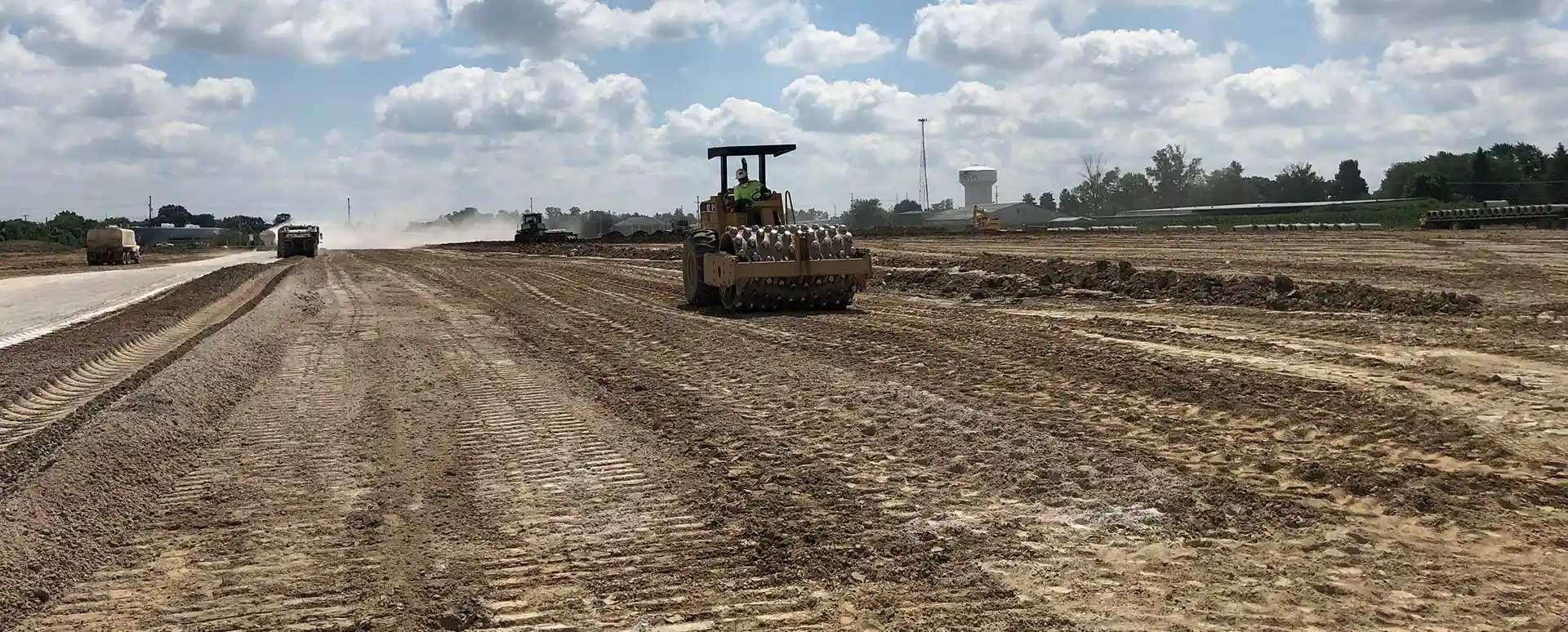
What is Meant by Soil Stabilization?
Soil stabilization is a process by which the physical properties of a soil are transformed to provide permanent strength gains before construction. Stabilized soils outperform non-stabilized soils when materials, design, and construction are properly considered. When the stabilized soil layer is incorporated into the structural design of the pavement, the subsequent layers can be thinner, resulting in sizable cost savings and minimizing the need for virgin materials. In addition to adding strength, stabilized soil forms a solid monolith that decreases permeability, which in turn reduces the shrink/swell potential and the harmful effects of freeze/thaw cycles.
Soil stabilization can improve in situ, or natural state, soils eliminating the need for expensive remove-and-replace operations. Often job sites where roads, building pads, parking lots, runways or other pavement structures need to be built contain naturally wet, weak soils. Those soils can be chemically treated to add strength through stabilization and improve engineering properties including moisture content and plasticity, through modification. Ex situ, or off site, soil stabilization processes are possible but are usually reserved for environmental projects rather than typical construction operations.
Chemical Stabilization of Soil
The chemical stabilization of soil is a relatively broad term that is used when chemical reagents such as quicklime, Calciment Lime Kiln Dust (LKD), cement, or other industrial co-products and bi-products are used to increase the strength of subgrade soil. Regardless of the reagent, the use of proper techniques is important. Thorough mixing ensures complete incorporation and an overall homogeneous mix. Moisture and compaction testing is important to be sure that all reactions have occurred. Each reagent must hydrate completely, and maximum density is only achievable at optimum moisture content. Regardless of the stabilizing agent used, pre project planning, including laboratory testing, is important to be certain that the proper amount of stabilizing agent is present to permanently stabilize the soil and provide the desired result.
Soil Stabilization Materials
Lime
Quicklime, often referred to simply as lime, is the chemical compound calcium oxide (CaO). Quicklime is available in two types, high calcium and dolomitic. High calcium is almost completely calcium oxide, whereas dolomitic quicklime contains a portion of magnesium oxide (MgO) along with calcium oxide. Some industrial applications such as steel need the magnesium component for certain processes. For construction purposes, high calcium and dolomitic quicklime are virtually indistinguishable. Learn more about why lime-based products are the most effective soil-drying agent and how they can improve soils through modification.
Lime will stabilize clayey soils to provide long-term, strength gains that will continue after initial application. Studies have shown that these reactions can continue for a year or more. Lime stabilization provides the calcium component and the proper chemical environment that is necessary to permanently stabilize a soil. Since lime is an alkali material, it provides the proper chemical environment by raising the soil pH to the point that naturally occurring pozzolans, such as silica and alumina, to become soluble. Once soluble, they are available to react and form cementitious bonds with the calcium from the lime. The resulting calcium-silicate-hydrates (C-S-H) and calcium-aluminate-hydrates (C-A-H) are permanent and reduce the effect of clay soil resulting in a very resilient subgrade rather than masking it as is the case with other stabilization techniques.
Soils with a plasticity index (PI) of 10 or more are generally great candidates for lime stabilization. Proper laboratory testing is important to determine soil reactivity and dosage rates necessary for proper stabilization.
Calciment® LKD
Lime Kiln Dust, or LKD, is a co-product of the lime manufacturing process that contains a combination of CaO, MgO and pozzolans. Much like fly ash, the pozzolans come from the fuel used in combustion processes and are finely sized materials carried by exhaust gasses and collected by emission controls such as bag houses.
These products are a hybrid of sorts between quicklime and cement that work well in 5-35 PI soils. The presence of pozzolans enables the stabilization of more granular, sandier soils. Since Calciment LKD also contains calcium, like lime, the product can also leverage the pozzolans naturally present in clayey soils to generate cementitious bonds. Similar to fly ash, anytime the co-products are used, energy consumption and emissions are reduced. The use of virgin material and disposal to landfills is minimized, making Calciment LKD an environmentally friendly alternative to traditional reagents.
Cement
Cement is a widely used composite material composed mainly of calcium, silica, alumina, and iron derived from limestone, sand and clay. All are processed, fired in a kiln and pulverized to a fine powder. When cement is exposed to water, it chemically hydrates resulting in a gel that forms an interlocking matrix around soil particles. The mix hardens, or cures, very rapidly, typically within one to three hours, so the soil-cement mixture must be placed, mixed and compacted quickly. This rapid curing results in high initial strength gains that taper off rapidly.
Cement is an effective reagent for stabilizing certain types of soils. However, not all soil types are created equal and understanding the geotechnical properties of the soils for your specific application is key. Cement is a good option when working with sandy, coarse-grained soils but the effectiveness of cement decreases as clay content and plasticity increase. Cement stabilization merely masks the effect of clay and is not an economical option to stabilize fine-grained soils. Additionally, undesirable shrinkage cracking is often associated with cement-stabilized soils allowing water to penetrate and cause further damage.
Soils with a plasticity index (PI) of 10 or less are generally candidates for cement stabilization. Proper laboratory testing is important to determine the right product, and dosage rates necessary to properly stabilize the soil for your specific application.
Other Stabilization Products
Bitumen
Bitumen is a naturally occurring organic binder that is typically obtained from petroleum distillation or refining crude oil. It is a sticky, viscous liquid that commonly holds asphalt together. When bitumen is added to a soil, it fills the voids in the soil to mechanically stabilize the soil rather than reacting with individual soil particles. Soil type is an important factor when considering bitumen for stabilization. Finely grained soils need higher dosage rates of bitumen to stabilize soil compared to sandy, coarse-grained soils. Bitumen is often one of the costliest construction materials, so dosage rates are a key factor for cost effectiveness when considering bitumen. Weather is another factor to consider as bitumen and its viscosity is very susceptible to differences in temperature. Viscosity will decrease with temperature resulting in poor mixing, an unwanted uneven mix and seemingly random stabilization in colder temperatures.
Geotextiles
Geotextiles are fabrics that resist chemicals and biodegradation. Like bitumen, geotextiles mechanically interact with the soil to provide increased strength and bearing capacity. Opening size, interlocking grab strength, and puncture resistance are important factors associated with geotextiles. The increased cost of geotextiles adds to the overall cost of the project.
Grout
Grout is a flow-able mixture of water, cement and sand that can be pumped throughout a jobsite. Slurried grout is injected at predetermined intervals to infiltrate the soil matrix. The mix cures over time adding strength and bearing capacity to the soil. Pressure grouting is only an option in granular soils as the material must be able to flow through the mass of soil. The fine particle size associated with clayey soils results in minimal to no permeation, rendering grouting ineffective.
Soil Stabilization Methods
Lab Testing
Laboratory testing is important to determine the product type and minimum dosage rate as well as the water necessary to reach optimum moisture content. Our Innovation Center and Customer Application Specialists are available to prove out options.
Transportation and Spreading
Lime typically arrives at the jobsite via pneumatic truck before being transferred into a spreader truck. Spreader trucks distribute the material on the job site at the specified dose rate. Once the chemical reagent is applied, water is usually added, and the amount is dependent on the desired results and current water content of the soil. For smaller or remote jobs, lime can be delivered in dump trucks or bulk bags.
Pneumatic Truck
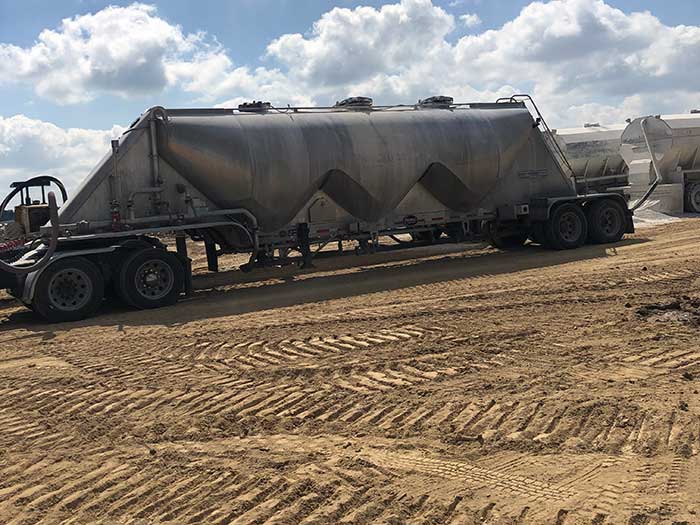
Bulk Bags
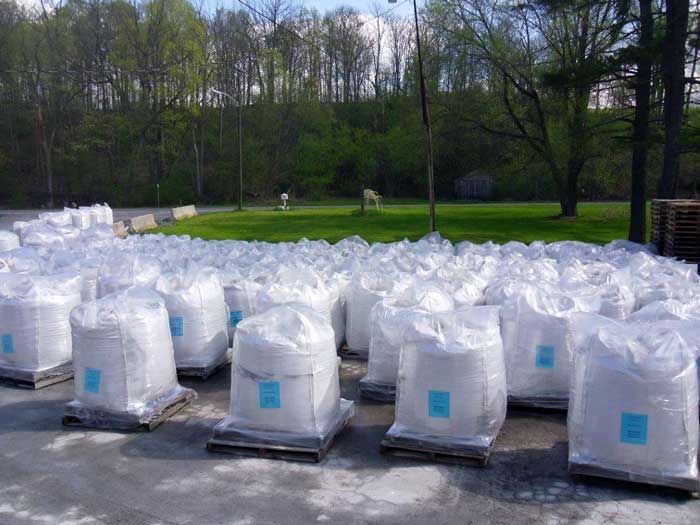
Mixing
The lime and water need to be properly incorporated into the soil to achieve a homogeneous mix and help break down the soil. Reclaimers are the preferred mixing equipment for this portion of the process. However, backhoes and bulldozers work well for smaller jobs or when the initial soil bearing capacity is low, which is often the case on environmental sites involving lagoon, sludge or sediment stabilization projects.
Compaction and Grading
Both compaction and grading are important to allow free water to drain to keep the integrity of the stabilized soil. Compaction, targeting maximum dry density, can be achieved by using a number of different soil compaction methods. The compacted material is then graded to a profile and cross slope. Finally, the surface is ready for a final smooth roll to seal the soil making the subgrade ready for further construction to continue.
Step by step process
Step 1:
Lime is transferred from Pneumatic truck to spreader truck
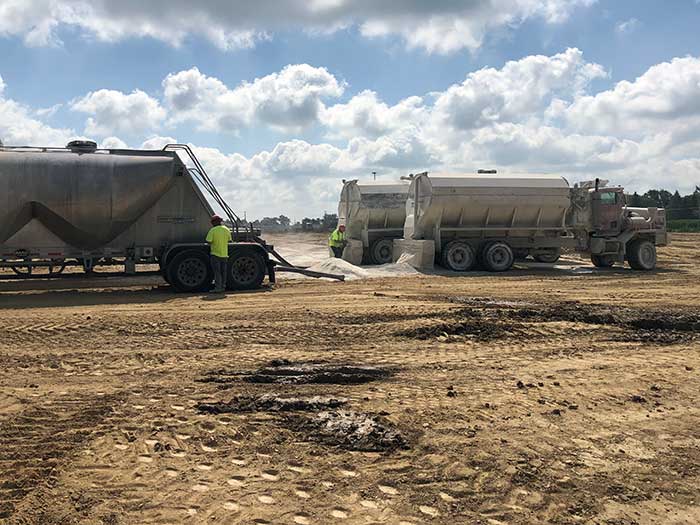
Step 2:
Mintek’s reagent, water and soil are mixed using a reclaimer
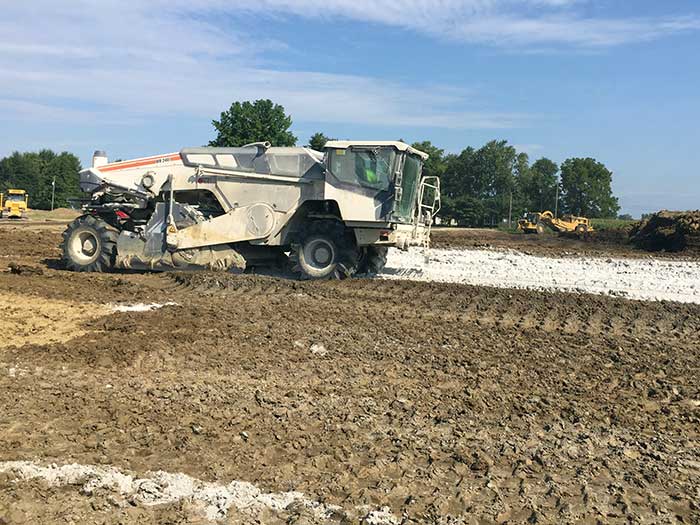
Step 3:
A spreader truck then spreads product over the problematic soil
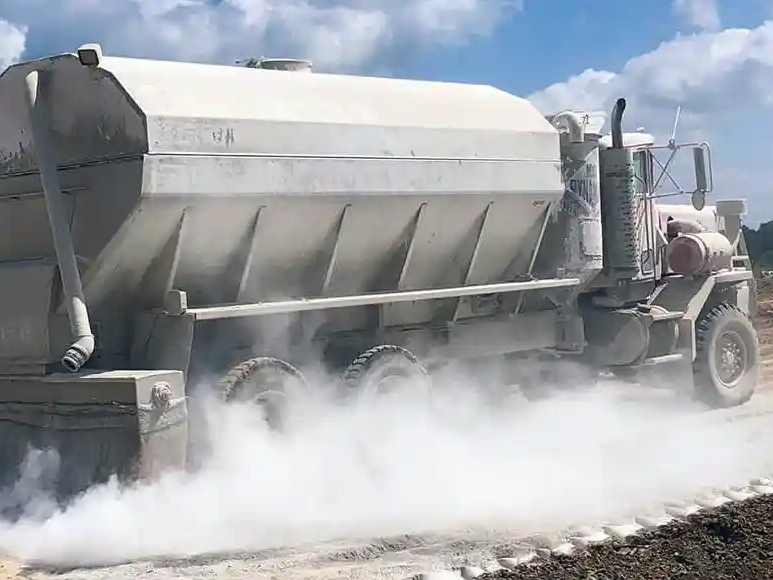
Step 4:
A drum roller or pad foot compacts the pulverized mix
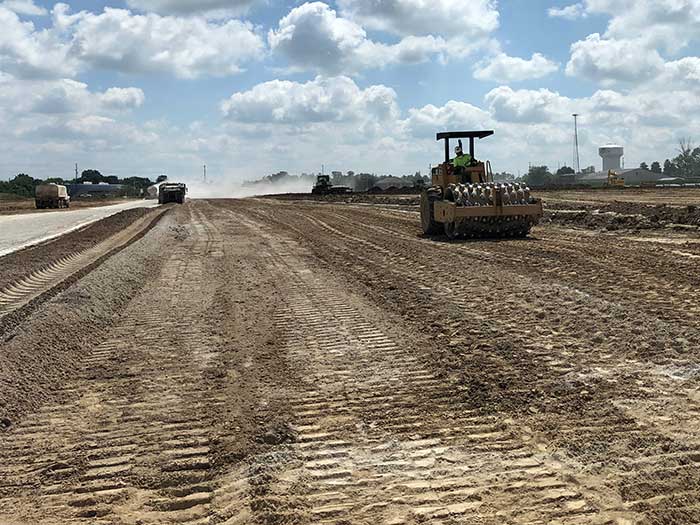
Soil Stabilization Using Cement
Cement stabilization is very similar to lime stabilization but the cement must be placed, mixed and compacted before the mix starts to cure, generally within three hours. If there is a disruption in production, reapplication and incorporation may be necessary.
We’re here to help you find the best solution for your next project. Let’s get started. Give me a call at 937-641-9901.

Josh Weser
Mintek Resources
Related Posts
Understanding Soil Stabilization with Cement and Lime
Creating a strong and stable foundation is essential when constructing buildings, roads, and other infrastructure. However, not all soils are naturally suitable for construction. Some may be too wet, soft, or prone to deformation and settling, which can lead to...
A Guide to Lime Soil Stabilization Specifications
Importance and Purpose of Lime in Soil Stabilization Lime plays a crucial role in soil stabilization, which is a process used to improve soil properties. The term lime is a somewhat catch-all term for many calcium-bearing materials, so it is important to understand...
Potential Pitfalls: Applying State DOT Standards to Small Commercial Projects
As a value engineering option, the importance of soil stabilization cannot be overstated. Soil stabilization lays the groundwork for stability, ensuring that structures remain steadfast against the test of time. Crucial to this process are soil stabilization...