How To: Applying Lime or Calciment LKD on a Jobsite
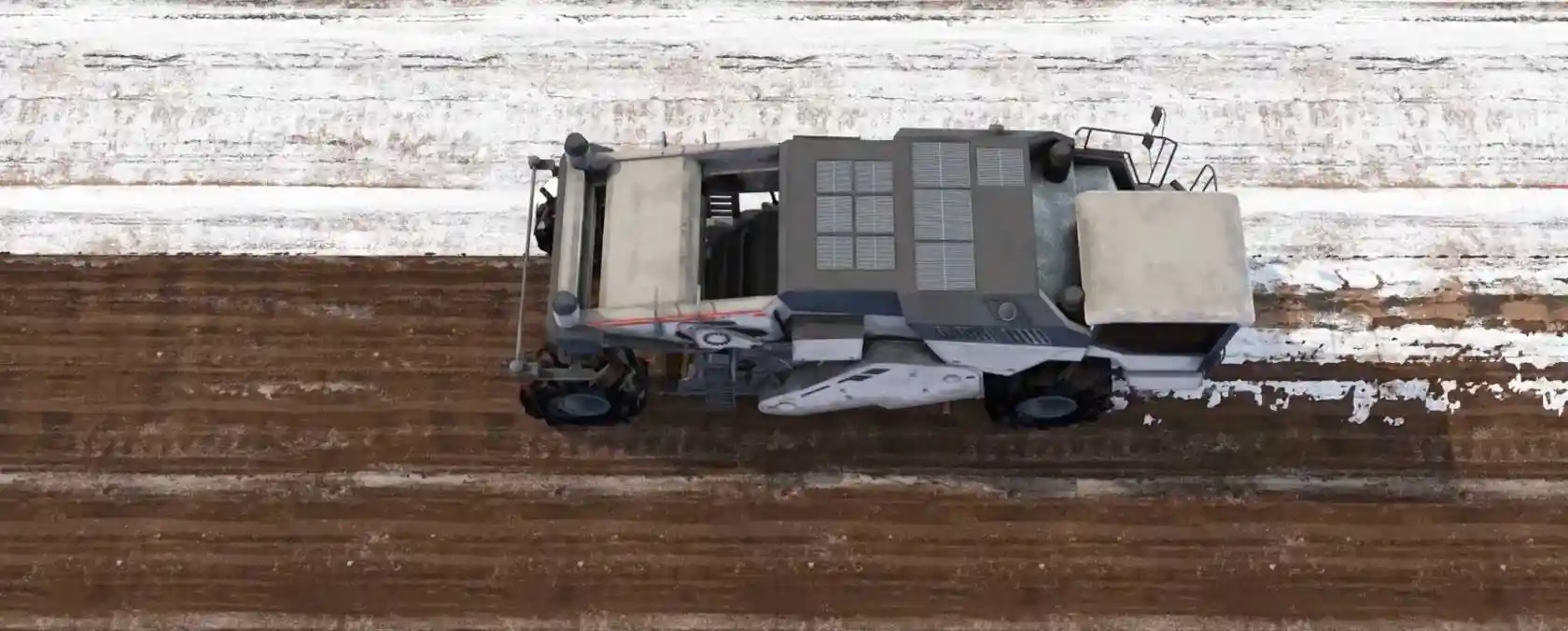
Interested in learning more about the most common ways lime or Calciment LKD are applied on a jobsite? Below, we walk step-by-step through the process.
Get back to work with less downtime
Transportation and Application
Most commonly, lime and Calciment LKD are transported to the jobsite via pneumatic tankers. However, depending on the jobsite needs, a dump truck or a flatbed loaded with super sacks can be used.
Once the material arrives to the jobsite, the material is transferred out of the pneumatic tanker into a site spreader truck with a large hose. After the material has been transferred, the spreader truck will apply the product to the wet, problematic, or unstable soil. Dose rates are dependent on soil conditions and geotechnical requirements.
Need help determining your desired dose rate? Check out our Dose Rate Calculator tool.
Mixing and Materials
A reclaimer, also known as a soil mixer or pulverizer, then mixes the calcium reagent into the soil to initiate a chemical reaction. Additional water may be needed if the soil’s water content is near or below optimum.
The addition of calcium-based reagents to problematic soils provides many benefits. As a calcium-based reagent is hydrated, a strong exothermic reaction occurs, driving off moisture within the soil. This also raises the pH of the soil, which provides stabilization with both short- and long-term strength gains.
Additionally, calcium ions released will modify the soil by reducing its plasticity, significantly reducing its shrink/swell potential.
Depending on the site conditions, mixing methods and materials used, a mellowing period may be necessary to ensure the material has fully hydrated prior to compaction. Mellowing periods vary based on site conditions, and averages around 4 hours. During this time crews can be working on other areas of the jobsite.
Once the reagent is fully hydrated, the soil can then be compacted, which is typically done by either a drum or pad foot roller. Once compacted, you will have an engineered subgrade that will provide the strength and stability to extend the life of your pavement structure.
We’ve Got You Covered
Save time and money on your next jobsite. Contact Mintek to learn more – 937-641-9901.
We're here to help you find the best solution for your next project. Let's get started. Give me a call at 937-641-9901.
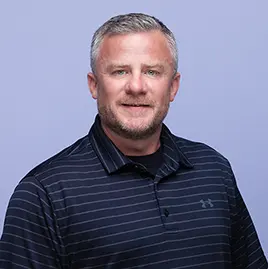
Josh Weser
Mintek Resources
Related Posts
Ground Control: Comparing Lime and Geosynthetics for Long-Lasting Stability
When building infrastructure on weak in-situ soils, a well-designed foundation is essential to ensure long-term resilience. Whether you're constructing roads, embankments, or industrial platforms, ensuring subgrade stability is critical—not just for performance, but...
Save Time and Money with Mintek’s Lime Stabilization Calculator
Lime stabilization turns challenging soils into durable foundations suitable for the construction industry. When lime-based reagents interact with soil, a chemical process alters its characteristics - binding clay particles, reducing plasticity & shrink-swell...
Exploring The Application of Lime Stabilization in Soil
Creating a stable foundation is essential for any construction project, yet many construction sites face challenges with unsuitable soil conditions. Lime soil stabilization offers a proven, cost-effective solution for transforming problematic soils into reliable...