Projects
VDOT I-81 Highway
Market
Application
Dose Rate
I-81 was the first U.S. Federal Highway FDR project. VDOT needed a long-term fix for a 3.7-mile stretch of road that was severely damaged due to heavy truck loads and high traffic. Calciment® was chosen as the stabilization agent because of the strength, stability and economic value the project needed.
Project Overview
- VDOT needed a long term fix to repair a severely damaged 3.7 mile stretch of I-81
- Previous surface-level fixes failed due to subgrade issues.
- FDR using Calciment LKD was chosen to strengthen and recompact the subgrade.
- The first U.S. Federal Highway Administration FDR project, and three years post-construction, the highway continues to perform well under heavy traffic
Background
The Virginia Department of Transportation (VDOT) needed to rebuild part of Interstate 81 in Augusta County Virginia after decades of high traffic volumes left a 3.7-mile stretch with significant damage. Originally completed in 1968, the road consisted of asphalt concrete (AC) over an aggregate base of compacted stone and soil. The existing subgrade had been built on top of impervious, plastic, clay soil without drainage. In the 40 years since the road had been built, truck traffic volume grew by 30% and truck loads increased significantly. These volume increases stressed the road to the point of failure. VDOT had previously repaired the road using milling and overlays; however the results were temporary and additional repairs were required every 6 – 18 months.
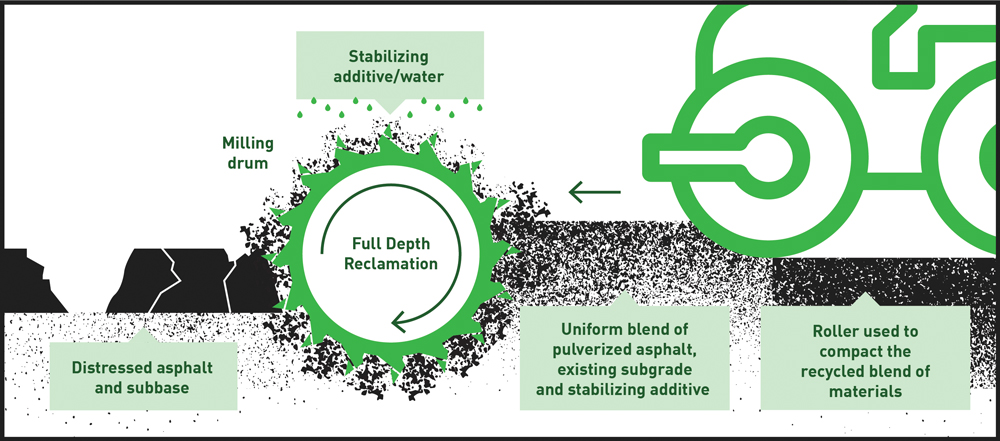
The Challenge
An initial evaluation revealed that much of the damage to the road was the result of inadequate base layers (the compacted aggregate and subgrade soil). The damage, known as bottom-up fatigue cracking, is often associated with loads that are too heavy for the pavement structure. Fatigue cracks allowed water to saturate the subgrade, further reducing load-carrying capacities. As the asphalt pavement structure flexed under traffic loads, the fatigue cracks in the base level worked their way up through the pavement. This condition can lead to deep rutting within the wheel paths that can affect skid resistance and even steering ability. Although traditional mill-and-overlay repairs provided a short-term solution, the underlying conditions remained and new cracks quickly surfaced. With only 8 months and a $7.6M budget, VDOT had to find a permanent solution that could be implemented economically.
The Solution
VDOT went to work to determine the best way to prevent premature failure of the base structure. Various laboratory tests were conducted on materials collected from the construction site; including: gradation, resilient modulus, indirect tensile strength, dynamic modulus, flow number, ride quality and rut-depth measurements. After reviewing the study results, a ground up approach was recommended to achieve long-lasting results. The approach consisted of three in-place pavement recycling techniques: full-depth reclamation (FDR) to strengthen & re-compact the underlying foundation; cold in-place recycling (CIR) to restore the asphalt layer under the driving surface; and cold centralplant recycling (CCPR) for the driving surface.
FDR was selected for the base layer to correct the severe structural defects that existed deep within the pavement structure. FDR most often consists of pulverizing, remixing and adding stabilizing reagents to the existing sub-base. FDR offers a host of benefits including lower project costs, an expedited schedule, and added structural benefits. In addition, roadways can be rehabilitated without full closure and extensive downtime. FDR reuses 100% of existing materials conserving virgin materials, preventing hundreds of tons of waste from going into landfills as well as fuel savings derived from not having to transport materials off-site for disposal.
Implementation
This project marked the first time in U.S. history that FDR, CIR, and CCPR were utilized together on a highway project. After testing several stabilizing agents for the FDR work, Calciment® LKD was chosen because of its ability to provide the compressive strength, stability and economic value that the project demanded. Calciment LKD was applied at a 5% dose rate to a depth of 12 inches after which the sub-base was compacted in place with padfoot and smooth drum rollers. Four to six hours after placing this new base, the contractors were able to top it with the recycled foamed asphalt mix from the portable plant which was used to pave a new flexible base course over the restored subgrade.
Results
The structural layer coefficients of the base layer were 0.37 upon project completion and continue to offer optimal results long-term. The innovative methods used by VDOT reduced construction time by two-thirds and saved millions of dollars. The entire project took only 8 months to complete & cost $7.6M. Traditional methods could have taken two years and cost up to $40M according to VDOT estimates. Savings were derived from less time on the job site, consuming less materials, and using less fuel to transport old and new materials to/ from the job site.
Field performance tests conducted 5 – 34 months post-construction revealed excellent ride quality according to VDOT criteria.
VDOT I-81 Highway